Bobinadores, rebobinadores, desbobinadores, enrolladores, desenrolladores, encarretadora, devanadoras; sea cual sea el término que utilicemos, estos sistemas se ubican todos en el manipulado de materiales en bobina. Constituyen parte de los elementos esenciales para realizar un correcto control de tensión mientras se procesa el material. Y esta regulación es crítica para mantener la calidad, y más teniendo en cuenta que los tiempos de aceleración, deceleración, carga y descarga deben minimizarse.
Un buen control de tensión garantizará la tensión correcta del material a lo largo de su recorrido en la máquina, independientemente de la velocidad o las condiciones de trabajo. La tensión, entendida como la fuerza aplicada al material en la dirección de la máquina, nos proporciona estabilidad dimensional del material. Dos factores a tener en cuenta para una tensión de trabajo óptima: estabilidad dimensional y riesgo de rotura. El control de tensión es necesario ya que la elasticidad del material puede cambiar de una bobina a otra. Una tensión excesiva provocará alargamiento del material en la dirección de máquina, y su estrechamiento en sentido transversal. En cambio, una tensión insuficiente encoge el material, dificultando un registro correcto, incluso sufriendo desplazamientos laterales sobre los rodillos de paso, la aparición de arrugas, todo ello complicando el proceso y comprometiendo la calidad del producto final. Muchos trabajos requieren un registro correcto del material para su impresión, troquelado, corte; y en operaciones de laminado donde debemos juntar varias capas de material la tensión debe ser la adecuada para evitar que el complejo se curve.
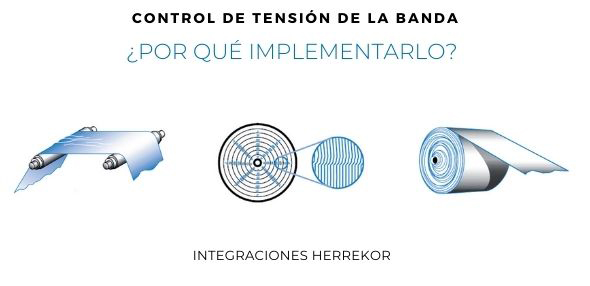
Es necesario controlar la tensión del material al introducirlo en la máquina, en el momento del desbobinado; y también en el momento de su salida de máquina al rebobinarlo. En ambos puntos un control de tensión deficiente puede resultar en bobinas telescopadas, descuadradas, arrugas, incluso roturas. Pero también en la zona intermedia de la máquina donde se produce el proceso puede ser necesario controlar la tensión.
El bobinado/desbobinado puede realizarse transfiriendo el movimiento a la bobina tangencialmente o a través del eje central. Para generar la tensión en el material actuaremos sobre dichas transmisiones. En el caso de transmitir el movimiento tangencialmente, la tensión la podemos generar en el material de manera periférica por medio de rodillos de apoyo, correas o ruedas, siempre que el material no sufra daños por este contacto. Entre los elementos utilizados -motores, embragues, frenos- también existen los limitadores de par magnéticos como solución perfectamente válida al tratarse de un sistema que trabaja a par constante.
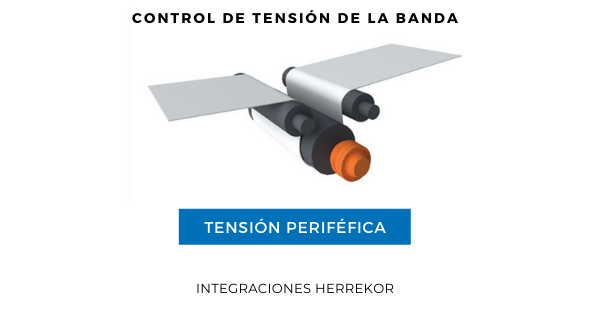
Pero la mayoría de materiales son sensibles al contacto y por esta razón, la técnica de bobinado/desbobinado más común transmite el movimiento a la bobina desde el eje central evitando así contacto con el material y permitiendo respetar sus características sin dañarlas. Con este método variamos el par de transmisión aplicado al eje de la bobina para mantener una tensión constante. Suponiendo una bobina de Ø1000 mm con un mandril Ø100mm, la relación entre el par máximo y el par mínimo sera de 10:1, y la relación entre el par y el diámetro de bobina es lineal. El objetivo es mantener la tensión constante tanto en el desbobinado como en el proceso del material. Pero al rebobinar el material aplicamos una tensión proporcional. Al generarse la bobina, cada vuelta deposita una capa que incrementa las fuerzas de compresión y que pueden provocar que las capas interiores -incluso el mandril- combarse o aplastarse. Una tensión proporcional alivia estas fuerzas al ir reduciendo la tensión del material a medida que crece la bobina.
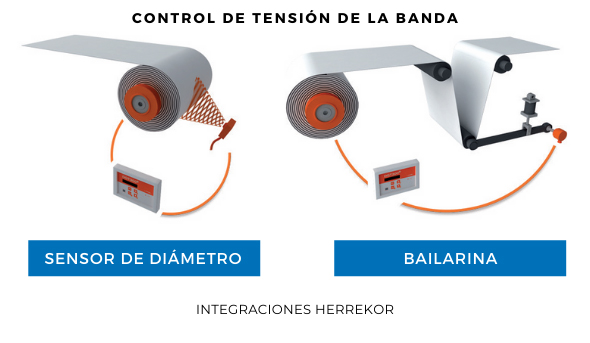
Precisamente en el desbobinado y rebobinado es donde más se complica el control de tensión debido a la variación constante de diámetro. Para esto existe una variedad de sensores que proporcionan una señal del diámetro de la bobina: sensores sin contacto por ultrasonidos o láser, por contacto con un brazo y potenciómetro. Pero basar el control únicamente en este parámetro sólo nos permite automatizar la transmisión tras ajustarla al inicio de cada proceso. Un sistema que permite controlar la tensión de manera que compense el diámetro, pero también cambios causados por empalmes, rozamientos, cambios de formato, es con el método de bailarina; asociado con un sensor de posición. Existen distintos diseños si hacen con un brazo oscilante, con sistema lineal o doble rodillo rotativo. Todos estos son adecuados en procesos de avance intermitente. Pero los sensores que ofrecen mayor precisión son las células de carga ya que tenemos un valor exacto de la tensión lo que proporciona máxima estabilidad en la tensión con respecto a la consigna aplicada.
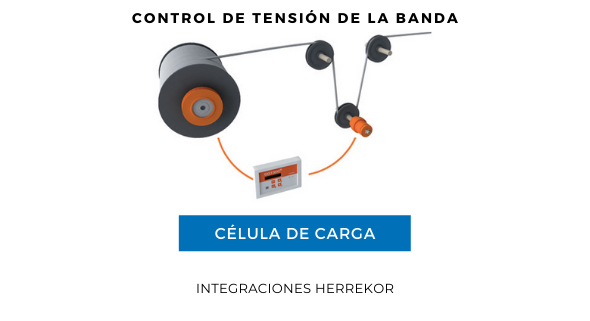
La unidad de control trabaja con estas señales, procesando los valores y de este modo proporciona la señal al freno, embrague o motor para mantener la tensión seleccionada. Si solamente utilizamos la señal de diámetro, tenemos un control de lazo abierto, que nos ofrece una precisión en la tensión del 10% y con un coste contenido. Mejor precisión obtenemos con los sistemas de lazo cerrado, bien sea con bailarina o bien sea con célula de carga. Las bailarinas trabajan típicamente con un ángulo ±30°, que combinado con un encoder de precisión nos puede dar la precisión necesaria para la condición de trabajo de diseño. Las células de carga actualmente proporcionan un rango de sensibilidad de 100:1 y una precisión ±0,3%; y cabe señalar que también existen con doble rango de sensibilidad 500:1.
Y ahora que ya tenemos el valor de la tensión, y con el control sabemos qué par debemos aplicar a la bobina, se la podemos generar mediante un freno, embrague, motor. Los motores ofrecen mayor precisión a mayor coste de adquisición y mantenimiento. Los frenos ofrecen un rango de par mucho mayor (180:1) que los motores (25:1), y aparte de un coste menor, también ofrecen un menor el consumo de energía.
Herrekor es un referente en la industria del converting desde hace más de cuatro décadas. Esta industria ha evolucionado durante este tiempo, y Herrekor ha evolucionado con ella. Mientras los fabricantes producen bobinas cada vez de mayor calidad y a mayor velocidad, los sistemas ofrecidos por Herrekor han pasado de ser una novedad a una necesidad. Y en ocasiones vemos que basta con mejorar el control de tensión, aprovechando las transmisiones existentes, para optimizar la calidad y el rendimiento de la máquina. Consulte con nuestros técnicos.