Bobinar múltiples bobinas en un eje puede ser todo un reto para conseguir la calidad de bobina deseada en cada una de ellas, pero gracias a los ejes diferenciales la tarea resulta mucho más fácil.
Supongamos que tenemos una bobina de 1200mm de ancho y lo vamos a cortar en bobinas de 90mm. Al intentar bobinar todas las bobinas en un mismo eje, todos los mandriles sujetos por el eje, veremos como giran todos por igual. Sin el sistema diferencial las diferencias de espesor en el material provocarán que unas bobinas sean mayores que otras, aunque sea 1-2mm en el diámetro (a veces hasta 10mm). El resultado es que las bobinas mayores sufrirán una tensión muy elevada, resultarán muy prietas, pudiendo suponer estiramiento del material, incluso llegar a romperse el material o que colapsen los mandriles. Y las bobinas menores resultarán con una tensión pobre, quedando sueltas, pudiendo telescoparse o incluso deshacerse.
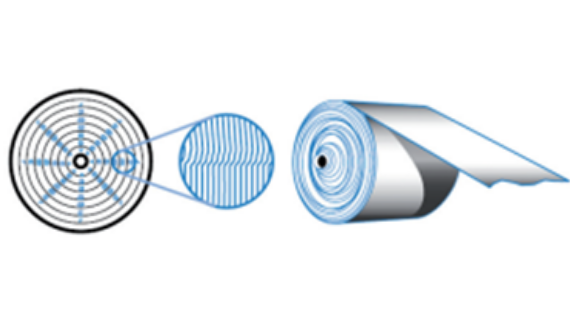
Las cortadoras-rebobinadoras más habituales son las dúplex de bobinado central. Estas se equipan con un sistema de rebobinado diferencial por el que cada bobina está aislada de las demás. Esto es esencial para bobinar de manera óptima materiales con galga no uniforme.
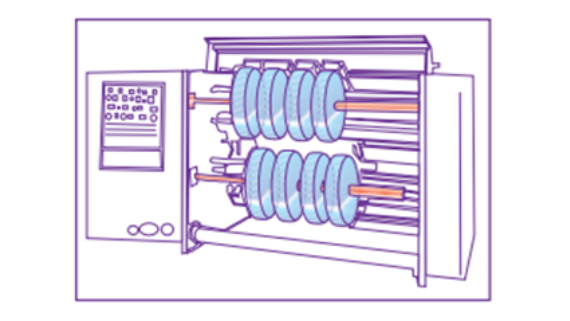
Existen distintos sistemas de bobinado diferencial. Cronológicamente la primera solución adoptada por el mercado consistía en un sistema que alternaba mandriles con distanciadores en cada eje. Este se combinaba con un sistema de presión neumático que ejercía una fuerza axial resultando en una compresión entre los mandriles y los distanciadores. El eje gira a mayor velocidad que los mandriles -estos retenidos por la tensión de sus bandas respectivas. Los mandriles y los distanciadores actuaban como embragues de fricción, proveyendo a cada mandril el par proporcional a la presión axial ejercida. Pero este sistema puede generar mucho calor en la zona de fricción, sobre todo por el área tan pequeña que tiene.
Posteriormente, el diseño del sistema diferencial evolucionó gracias a la llegada de los ejes expansibles de chaveta larga. Las chavetas utilizadas para sujetar las bobinas se sustituían por materiales que permiten la fricción directamente con el interior de los mandriles. Regulando la presión en las cámaras de aire que expanden las chavetas, se controla el par de transmisión en los mandriles y de este modo podemos regular la tensión. Este sistema requiere de la utilización de mandriles de alta calidad, y aun así tienden a generar polvo.
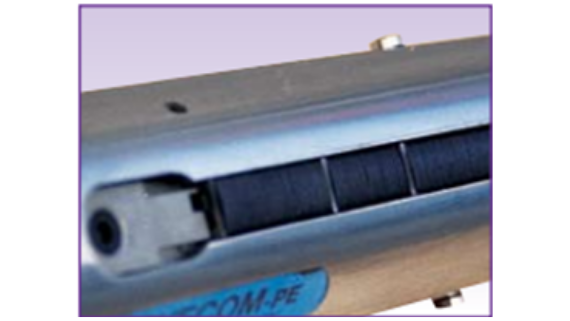
Por último, tenemos los ejes diferenciales constituidos por casquillos. Estos casquillos expanden en el exterior de modo que sujetan los mandriles por su interior, evitando así deslizamientos de la bobina sobre el eje. Es en el interior del casquillo donde encontramos el sistema de fricción que regulamos por medio de la presión neumática de unas cámaras internas diseñadas para esta función. De este modo podemos variar el par de transmisión y por ende controlar la tensión en las bobinas.
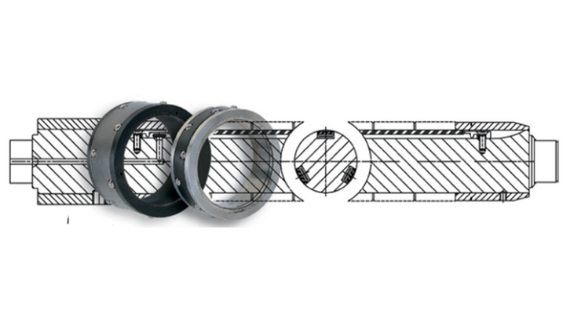
A medida que rebobinamos el material, el diámetro de la bobina incrementa y requiere de una variación del par de transmisión en el eje para mantener la tensión constante. Esta regulación la realizamos variando la presión de aire en el eje. Esto implica tener un sistema de alimentación neumático regulable continuo. Los valores de presión iniciales varían en función de la tensión del material tal como vemos en la tabla 1:
Presión neumática (bar) |
Tensión (N/cm) |
0,4 – 0,8 |
5 |
1,0 – 1,9 |
10 |
2,0 – 2,5 |
15 |
2,8 – 3,3 |
20 |
Tabla 1: Valores de presión iniciales habituales
El bobinado diferencial requiere que todas las bobinas deslicen. El eje diferencial debe girar a mayor velocidad que la velocidad de línea. Para obtener la misma tensión en cada mandril, cada uno de estos debe patinar en función del espesor del material en cada bobina. Aquí entran en juego los mandriles. Estos deben ser de buena calidad y tener una pared mínima de 10 mm. El diámetro interior debe tener una tolerancia de ± 0,2 mm para obtener un bobinado uniforme.
La mayoría de aplicaciones requieren de una sobrevelocidad de 3%-10%. La variación del espesor del material determina el valor de sobrevelocidad. Para un material uniforme la sobrevelocidad necesaria es pequeña, mientras que si tenemos variaciones importantes en el espesor del material la sobrevelocidad deberá ser más elevada.
Para controlar la sobrevelocidad debemos conocer la velocidad de línea y el diámetro de la bobina. Con un encoder podemos obtener una señal y con un sensor ultrasónico la otra, respectivamente. Con esta información podemos mantener una sobrevelocidad constante, teniendo en cuenta que a medida que crece la bobina el eje reduce su velocidad.
Como se desprende por lo comentado, el control del motor de bobinado de la máquina debe realizarse con un control de velocidad y no con un control de par.
Otro elemento que entra en juego y al que hay que prestar especial atención es el rodillo pisor, empleado para eliminar el aire que se introduce entre las capas de la bobina. Debemos tener en cuenta que estos rodillos crean tensión en el material y por tanto un exceso de presión creará una tensión que el eje diferencial no podrá controlar. Por eso la fuerza ejercida por el pisor debe ser la mínima necesaria para eliminar el atrapamiento de aire. También es importante su paralelismo con las bobinas: un rodillo que no sea paralelo provocará presión en las bobinas y reducirá su calidad.
Herrekor es un referente en la industria del Converting desde hace más de cuatro décadas. Esta industria ha evolucionado durante este tiempo, y Herrekor ha evolucionado con ella. Mientras los fabricantes producen bobinas cada vez de mayor calidad y a mayor velocidad, Herrekor ha pasado de presentar el eje diferencial como una novedad a considerarlo un standard. Pero en continua evolución. Concretamente en lo referente a los casquillos de los ejes diferenciales, SVECOM ha desarrollado una nueva generación de casquillos tanto en acero con mayor ajuste de las esferas logrando conferir mayor estabilidad en la bobina, incluso con anchos mínimos. Y también casquillos en plástico para materiales de pequeño espesor. Esto permite disponer del grado de sensibilidad idóneo para obtener un resultado óptimo.
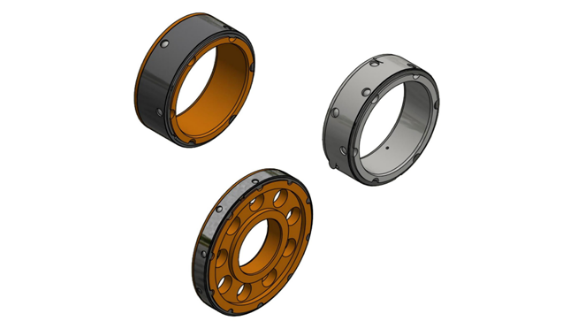
Hemos mencionado al principio que este sistema equipa las cortadoras-rebobinadoras dúplex de bobinado central. Pero su instalación no está reservada exclusivamente para la maquinaria de nueva construcción: también es posible adaptarlo en máquinas existentes. Sabemos que en algunos sistemas de bobinado puede ser difícil alimentar con aire constante el eje. Svecom dispone de soportes de seguridad con toma para alimentación de aire. Consulte con nuestros técnicos para ampliar la información.